Process water from factories is a burden for businesses because of the money spent treating the wastewater and complying with regulations but Hong Kong-based startup iCell Sustainable Nutrition aims to change this. Its proprietary technology helps companies in food and beverage manufacturing turn their process water into revenue streams instead of expenses.
In these industries, water is widely used for cleaning, scalding and other operations. As it washes away, it carries bits and pieces of food, resulting in wastewater rich in nutrients. iCell can upcycle these nutrients to make single-cell proteins (SCPs) for use in animal and aquaculture feed, plant fertilizer and food and healthcare products.
The upcycling process also cleans the wastewater, allowing it to be reused or discharged without polluting the environment. Chinese sugar refinery Shandong Zhonggu Starch Sugar Company, a client of iCell, uses the technology to reprocess 10,000 tons of wastewater per day. It no longer has to pay $300,000 a year for wastewater disposal. It can also earn additional income from the sale of SCPs.
iCell was founded in 2011 by Colorado-based biotech player Nutrinsic and Gentech, a Shanghai-based animal feed company that operated Nutrinsic’s projects in Asia. iCell’s solutions were built on patented technology developed by Nutrinsic that allows SCPs to be produced from nutrients in food and beverage plant wastewater. iCell now owns this technology, having acquired Nutrinsic in 2018.
The company operates three commercial-scale facilities in China and has multiple ongoing projects in the US and Europe. It holds more than 50 patents for the production and use of SCPs and says it has sold tens of thousands of tons of SCP products. iCell has received undisclosed funding from IDG, SLC Holdings, Artiman, BDO and Lighthouse Finance IDG.
Resource and energy efficient
iCell describes its solution as “a combination of microbial growth, cell wall extraction, enzymatic fractionating and protein concentration techniques.” It involves a fermentation process, where the nutrient-rich wastewater is fed to protein-producing bacteria. The bacteria eat the organic nutrients in the wastewater. The aerobic bacteria are then harvested, dried and sterilized and used to make SCPs.
This process not only cleans wastewater but also helps avoid greenhouse gases. Without it, the carbon-based nutrients in the wastewater would decompose and generate methane, a greenhouse gas that is 25 times more harmful than CO2.
According to iCell, for every acre one of its facilities takes up, it helps to avoid carbon emissions equivalent to 10,000 cars on the road. Making SCPs from upcycled nutrients is also resource-efficient. For example, an iCell facility can produce 500 tons of protein per acre whereas, producing the same amount of soybeans requires 350 acres. iCell’s process also uses less than half the energy required to produce proteins from algae, fish or soybean.
Last December, iCell formed a long-term partnership with CP Henning, a wholly-owned subsidiary of Charoen Pokphand Group (CP Group), to produce SCPs in China with wastewater from CP Group’s agricultural and animal husbandry food enterprises.
Commenting on the deal, COO of CP Henning Li Sumei said iCell’s solutions would allow the CP Group to produce SCP for use in its feed mills from wastewater discharged from its food plant while using the clean water for rinsing and washing in its workshops. This “will eliminate pollution, reduce carbon footprint and operating cost, and realize a profound dual-circulation of nutrients and water,” she added.
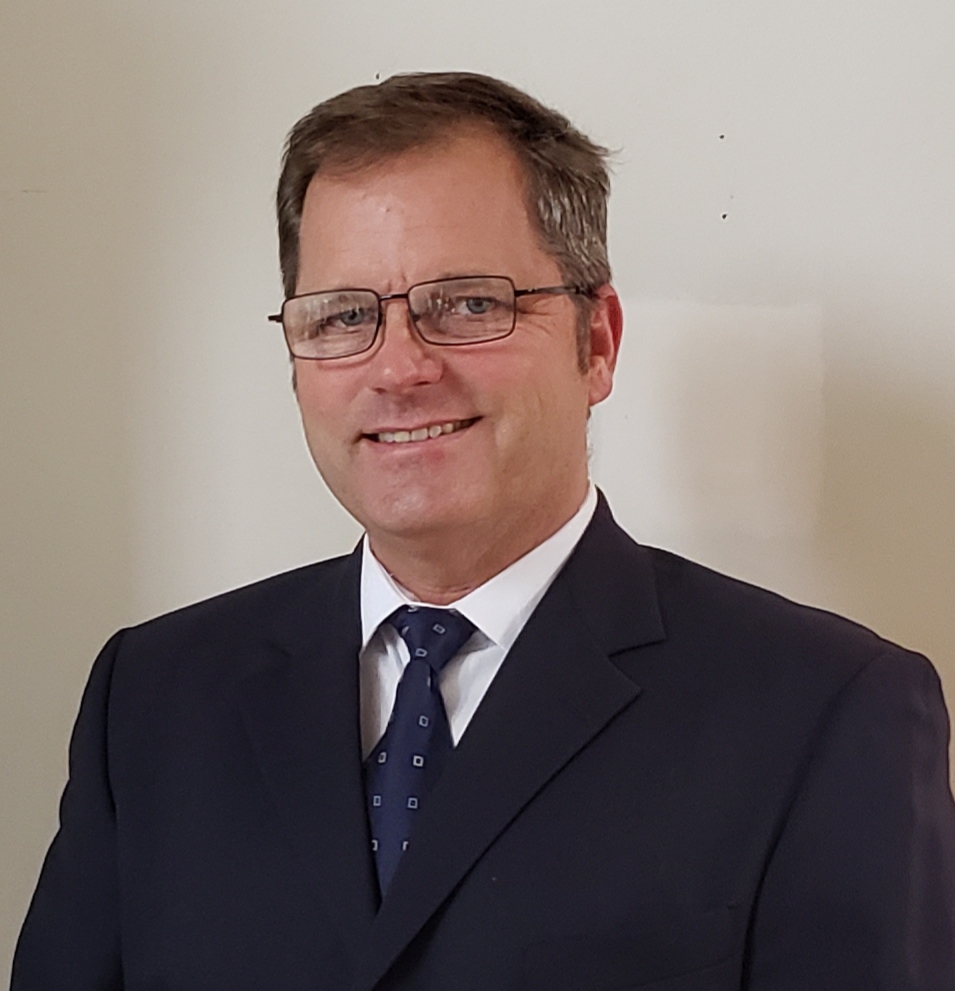
iCell has also developed a modular production system called MiCell, which requires a small investment of about $1m. It has completed several site evaluations of large-scale food plants worldwide and has found 100 companies where it would be feasible to produce SCPs by recycling their wastewater using MiCell. Thirty projects are expected to be operational in the next three years.
New aquaculture model
iCell has also developed a land-based recirculating aquaculture system based on its existing technologies. The system integrates seafood farming and seafood production, converting what would have been organic waste into a valuable protein feed ingredient and using the clean recycled water for SCP production and aquaculture.
CEO Mark Rottmann explained this move at a Future of Fish Feed (F3) Challenge panel discussion in April this year. According to him, the market is flush with cash, but investors are looking for big-ticket items in the tens of millions rather than small $5m investments here and there. “So we’ve taken a new approach by integrating iCell with aquaculture, creating a business model with more synergy and larger investment in [the range of] $30m–$50m per site,” he said.
"We're going after premium aquaculture species like eel and yellowtail and targeting sites with at least 1,000–2,000 tons of [annual] aquaculture production,” he added at the Future Food Asia 2021 conference in June.
iCell is currently seeking to raise about $50m to grow its land-based recirculating aquaculture business in Europe and the US, where Rottmann feels “consumers are prepared to pay for…premium [aquaculture] species that are sustainably produced.” ICell has begun working with an unnamed 1,000-ton eel aquaculture operation to apply its technology in a pilot project in the US.
“Local authorities and site partners want to see it in action with their own eyes before going ahead with approvals,” Rottmann said.
Meanwhile, iCell has also entered Europe, collaborating with Swedish aquaculture player Quality Salmon to integrate iCell’s land-based recirculating aquaculture system into what will be the largest salmon farming industrial park on the continent. Still under construction, this sustainable land-based salmon farm is expected to operate on a 140-hectare land site and produce 100,000 tons of salmon per year.