In late 2017, a group of engineers and construction and building experts came together with one common objective: to disrupt one of the world's least-disrupted industries – their own. Three years later, the startup they created, Modulous Tech, is showcasing the first pilot of its pioneering technology: an end-to-end generative design and delivery solution for affordable, sustainable and modularized housing.
An industry rife with inefficiency, waste and unsustainable practices, the real estate and building sector also faces ever-increasing housing shortages and sky-high costs. To come up with a solution that addresses these problems, Modulous’s six-strong co-founding team drew on more than a century's worth of combined relevant experience, including architectural design, project management, building sustainability and building safety.
Combining an AI generative design software with a defined kit of parts, Modulous’s platform enables modularized unit assembly in just a few hours, saving months of project development work. Automated procurement and an integrated, localized supply chain also significantly contribute to environmental sustainability.
This month sees construction begin on a pilot project of 30 affordable apartments and a community center in the London Borough of Lewisham funded by the Greater London Authority. Modulous is currently undergoing a bridge funding round for an undisclosed sum before its planned Series A funding round next year.
Soon after its founding, the startup secured £1m in seed funding led by US investor Blackhorn Ventures, which specializes in supporting sector-transforming startups. It also secured funding from CEMEX Ventures, the CVC arm of the Mexican building materials giant; and from UK-based family office investment firm Goldacre, which is part of asset manager Noé Group. Goldacre runs the proptech accelerator RElab that Modulous joined last year.
In 2020, Modulous was a finalist at Madrid's virtual South Summit. Among other construction sector nominations, it was also a finalist out of 200 entrants in the 2019 Tech for Good category at the real estate industry’s innovation competition UK PropTech Awards.
CompassList recently interviewed COO and co-founder Christopher Mortensen about Modulous's unique product and its implications for bringing scale to residential design and planning, and more.
This interview has been edited for length and clarity.
What prompted the idea for Modulous? Did you know initially what shape the tech would take?
When the original co-founding group came together, we had all noticed the inefficiencies in the construction industry. Whether in the design process or in construction, there are inefficiencies across the board. We also saw that sustainability was a big issue: 30% of the materials that are brought onsite end up in landfill. Waste is a huge problem, and that's confirmed in research by bodies such as the World Economic Forum.
We were tired of being in an industry that just hadn't embraced technological disruption to better itself. We're seeing changes now. Within the investment space, we're seeing proptech and construction technology becoming increasingly important and larger firms are starting to look at technology in a broader way to help solve problems, whether it's design or in construction. So there's a recognition that our industry needs to innovate. It's just behind others.
The original idea was to start to look at how we could digitize ourselves and digitize our process. But we quickly understood that in order to make real strides in permitting the design and delivery of more sustainable homes, we needed to create something that was end-to-end across the whole value chain. Otherwise, we would just be producing a kind of point solution that solves only one cog in the machine where greater inefficiencies still exist.
To make real strides in the design and delivery of sustainable homes, we needed to create something that was across the value chain
Were London's sky-high accommodation costs and shortages a main motivator in getting Modulous off the ground?
Exactly, though it's not just London but the UK in general, where we've got a 4m backlog in homes. And depending on whose white paper you read, whether it's the central government or some of the educational institutes that study these things, the deficit is growing by somewhere between 100,000 and 140,000 homes per year. So our industry is fundamentally failing to provide the housing that this country needs.
However, the UK is not alone. In the EU, the backlog is 8m and in North America it is upward of 10m. So there's a huge, huge need – and a lot of that is in the affordable housing sector. The most vulnerable people are the ones that are having the hardest time finding housing.
Modulous's tech was developed entirely in-house. What exactly does it consist of?
In order to be an end-to-end solution, we developed two pieces of technology. One is the software that allows us to generate designs very rapidly and the other is a physical product that is embedded in that software.
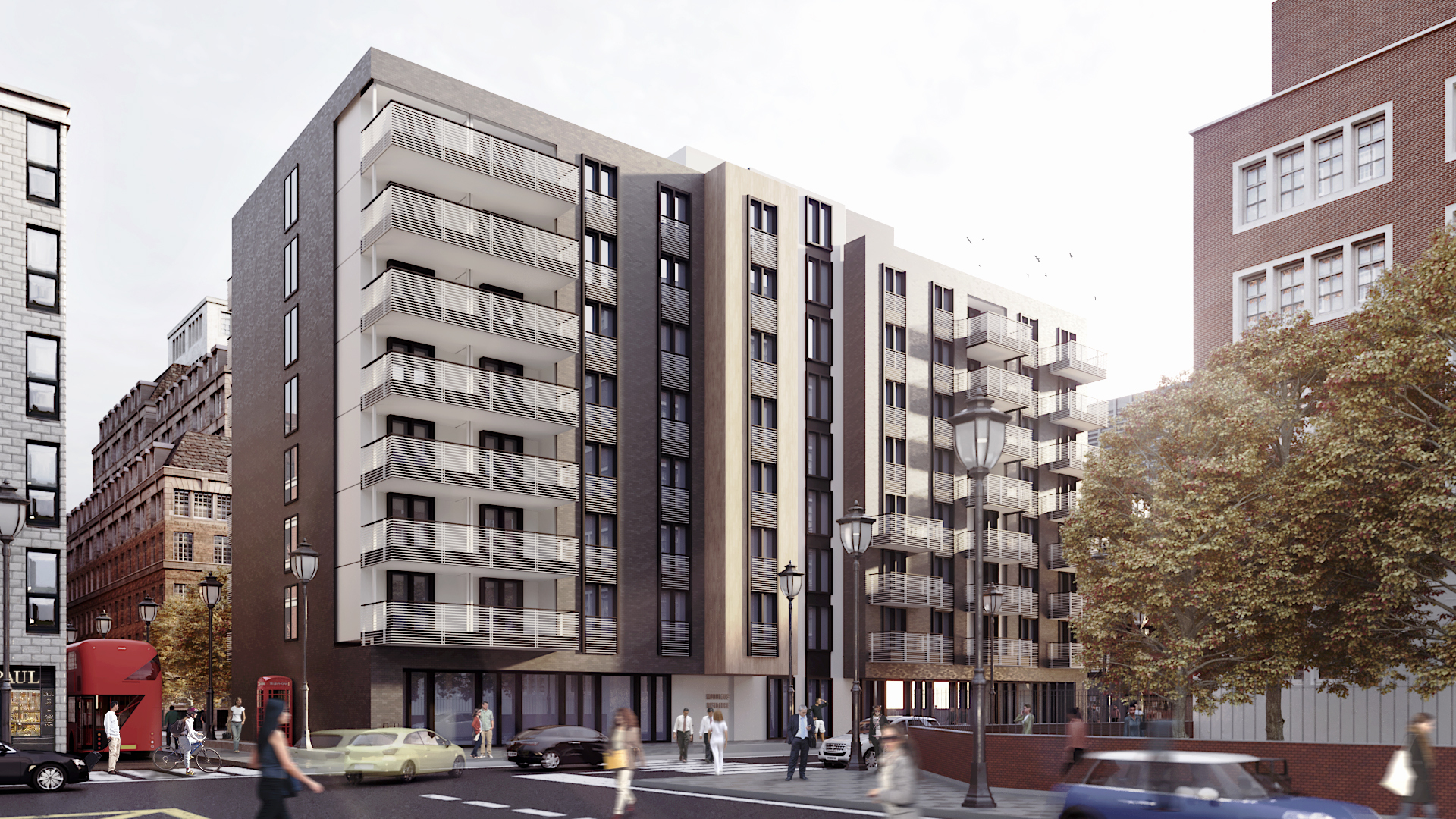
The first essential element for us was having a physical kit of parts [a module-based, deployable construction system], because without that we couldn't build the software. A couple of things in that kit-of-parts that were really key were speed of assembly and health and wellness performance.
We have married the two elements to efficiently create a value chain to deliver on affordable, sustainable housing. It minimizes the inefficiencies that you have from handing a design to somebody and the contractor having to redesign elements or modularize it – and all the other kinds of inefficiencies that happen that every time there's a handover of work.
From our standpoint, it became apparent early on that our business wasn't going to be just a software-based business but an end-to-end solution provider. So we'll come in at the very beginning and work with clients on the design and feasibility of projects, right through to delivering the project on-site. We don't yet have stand-alone software that we allow others to use. That will come with the evolution of our business.
When we look at performance, we're trying to move toward carbon-neutral standards using Passivhaus as a standard [an international energy performance standard drastically reducing the requirement for heating and cooling].
What is the kit of parts' composition and functionalities?
The most important factors are that it can be assembled really quickly. We’ve got unit assembly down to one hour and four minutes at the last count. It’s also critical that it performs excellently from an energy and thermal standpoint and that it's high-performing from a health and wellness perspective.
We’ve got unit assembly down to one hour and four minutes
It is a standardized physical kit, meaning we deliver modules to the site. Our modules can vary in height, width and length, with the layout customizable to the client's needs.
So if they want to go for UK National Space Standards (NSS), or if they want to have something that has different space standards because it's for adults with autism, we can do that as well. What we don't have is pre-described plans that you have to buy off-spec. Our kit of parts allows us to design within constraints.
We use high-performing materials that are available to any contractor – we recognized early on that Modulous is changing so much in traditional construction that fundamentally changing everything might be a step too far. There's a huge benefit in using materials such as biocomposites, instead of traditional steel frame structures, from a carbon-neutral perspective. But there's also an adoption risk that we need to get over before we can start to push the industry toward changing everything.
Our way to help minimize waste is to standardize the way we construct layouts. In practice, this means that rather than having walls of any size, our walls are based on increments of standard board widths. We can go down to half boards and quarter boards, and that allows us to utilize off-cuts so we're not cutting panels into strange shapes, and then throwing the leftovers into the skip.
We do have an R&D platform that runs in parallel with our first version of our kit of parts to improve it and become more sustainable. Some of the materials that our technical director is looking at include more biodynamic materials such as mycelium-based insulation that you can grow, and mineral-based insulation products.
Within our team, there is a deep understanding of things such as sustainability and fire-and-life safety, so we've designed our physical product to be an exemplar in the market. We’re looking at features such as installations and don’t want to repeat the tragedies that happened at Grenfell Tower or any other fires by using anything flammable. Our aim is to create spaces that are healthy and remove toxic materials that are on the Red List of harmful substances, including VOC's.
What about the role of the software? How does it work?
The software is designed to work with a client who is a landowner or a developer, but who might also be a housing association or a local authority. Our software package allows us to move beyond just a concept design by using a generative design methodology that utilizes our standard kit of parts. This methodology utilizes the local codes and regulations, whether that's London or Bristol or wherever, plus the NSS, the budget and the client brief, e.g., the mix of one or two bedrooms or the need for ground-floor amenity space.
Our generative design engine creates optimized designs according to those three rule sets that are designed around the kit of parts. Without this kit, you only have a concept design but you rapidly have a detailed design once you add a construction methodology. Combined with the supply chain that we have, we can go very quickly from an idea with the client to a pretty robust cost plan.
So we are getting to a place where rather than going from an idea to a design in 9-12 months with a traditional design team, we can do so in a matter of days and weeks. Before Modulous, we worked individually on these types of projects for decades and we know what goes into these conversations and how to optimize for solar exposure, thermal performance, overheating and all these things.
Effectively, what we're doing is codifying all that and utilizing computational power to make those comparisons and decisions quicker than then we physically can.
Are all of your designs residential apartment blocks?
Functionally, we're looking at affordable multi-family, multi-story residences because of their efficiency in terms of space and sustainability. For a single-family home, our cost points are probably too high.
We're in our pilot year and our first project is for 30 units of affordable housing in Lewisham in southeast London, plus a community center funded by the Greater London Authority. We'll be breaking ground on that any day now. We are also working on an affordable housing scheme in Bristol with Bristol City Council from the earlier pre-planning stage.
Another essential part of your offer is a commitment to optimized supply chains and local assembly.
Yes. The software identifies who the local assemblers are. This is a key piece to our business model. We work with regional partners to assemble the units for two reasons. One is sustainability – we didn't want to be trucking big units around the country – but we also want to promote local employment and didn't want to create something that does not add to employment in that local area. So as we're developing and going into new regions, one of the first things that we do is to identify potential local partners.
Our assemblers are delivered a flat pack of floor, wall and ceiling assemblies and their job is to erect the internal and external walls, utility cupboards and to put the roof on. Our wall panels are all pre-wired and pre-plumbed and we utilize things such as pre-packaged utility cupboards. A module can now be built physically in about an hour, meaning just the physical build of internal and external walls. We think we'll get that down to about two-and-a-half to three hours to build a complete module using four workers.
We work with regional partners to assemble the units for sustainability, and to promote local employment
Can you explain your current and future business models?
We are currently project-based, designing and delivering projects for developers. But we see that moving toward being product-based.
We anticipate that we will have portions of our software that are usable by external parties by the end of this year. It won't be full-suite – it might be feasibility tools, allowing developers to assess sites. We're developing our rollout map of that.
At the inception of this, we intended the digital component of the business to be an internal tool as opposed to an external tool. Over the course of the last two years, it became quite apparent that what we are creating isquite attractive to external parties, whether they were developers or councils or design teams.
Though our first business model is with us as the home builder utilizing technology, our next iteration will be a franchise methodology, where we have all the processes, the design software and the robust supply chain in place for somebody else to pick up and self-develop.
So if you're a council, housing association or a developer, you will be able to develop the housing yourselves using our system. That will be the next version of our offer. Off the back of that, if you're only interested in the software, we will enable it as a standalone product.
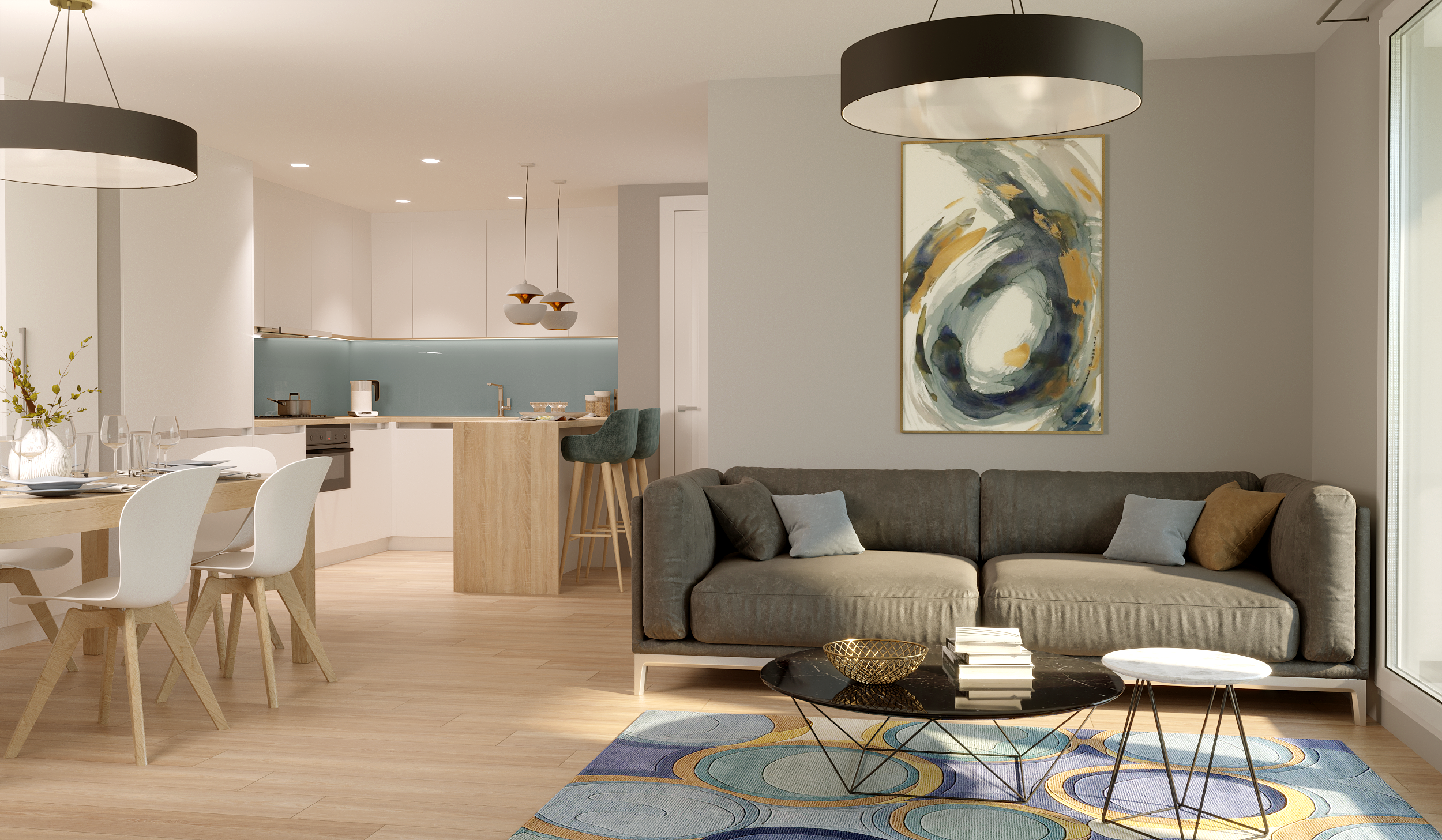
Do you have any direct competition? Are developers open to modularized housing?
In terms of generative design, there are some great platforms out there, but they are not competitors in the traditional sense because we've joined a digital technology product to a physical technology product. Because they [the generative design platforms] lack construction methodology, in my view, they are concept design tools that still get passed on to traditional design teams afterward. There are not many modular providers. I don't think we've seen any that are using the distributed assembly methodology that we use.
We see the traditional homebuilders as our competitors. Because we've got a huge housing deficit, we see others in the modular space as peers and we want them to succeed. Also, becausemodular players in this country are also trying to push back against negative perceptions of being post-war pre-fab structures. We are trying to move toward attitudes in the Netherlands and Germany, where modularized buildings are perceived as highly engineered and crafted.
We won't be able to make the shortfall of 140,000 homes alone, but if we have a franchise model that allows housing associations or local authorities or developers to do that, they can collectively start to make a bigger dent in that deficit year-on-year utilizing our system.
What do you see as the potential role of Modulous's tech in the future delivery of affordable accommodation internationally? What are your plans in this area?
I think technology is going to play a huge part in driving toward sustainable net-zero designs at a pace that would otherwise not be possible. We've got global commitments to get to net-zero ranging from 2030 to 2050, and I think our software will add to that overall value in being able to achieve this.
In countries such as the UK, the EU and North America, where there are high labor costs, the off-site way of construction allows us to avoid having hundreds of people on site. In other markets where labor is not a driving force in terms of cost of project, it becomes more difficult.
We’ve had discussions in Ghana, Nigeria and India, and those markets are much harder to deal with in terms of a cost-saving, off-site project because their labor rates are very low. In those markets, our software could allow for better design solutions while they still use their traditional on-site methods.
In terms of expansion, we're looking to the EU. One of our founders, Markus Cosmann, is based in Vienna so we're looking at projects through him. Blackhorn Ventures, our lead investor in our seed round and based in Denver, would love us to make moves toward North America.
We also have eyes on other mature markets that have robust supply chains. One of our angel investors is based out of Singapore, and we talked about launching some sort of version of our product there.
We just have to be careful about not overextending ourselves too quickly and making sure that our quality is upheld across all of our product ranges.