Two years ago, Robert Luo visited his uncle’s dairy farm in China and experienced a hidden reality of that business: the accumulation of spoiled milk that was going to waste. Was there a way to turn his uncle’s losses into profit? Luo returned to the US committed to finding an answer that could help over 600,000 dairy farms in China and potentially the rest of the world.
Indeed, an estimated 128m tons of milk is wasted every year due to overproduction. The situation has worsened amid the Covid-19 pandemic, which has impacted global supply chains and highlighted inefficiencies at the heart of our modern food production system. Schools and cafes, some of the biggest buyers of fresh milk, temporarily closed during the Covid lockdowns, leaving farmers with a sudden surplus of milk.
At the same time, the cows still had to be milked. At such short notice, the milk couldn’t be turned into other products, like cheese, either, because of limited processing capacities and cold storage. Farmers ended up having to dump millions of gallons of milk away – 3.7m gallons daily in the US alone.
After a year of research, Luo and his friend, Daniel Zhuang, founded Mi Terro, an LA-based startup creating eco-friendly fibers from food waste based on a circular economy model. These fibers can be used to make sustainable cotton-alternative garments, as the Mi Terro process uses 60% less water than organic cotton production and at a cheaper price. The same raw material can also be processed differently and used to create environmentally friendly packaging films that substitute plastic.
Mi Terro tackles issues at the root of the world’s second most polluting industry, fashion, as well as plastic contamination. Luo sold his very first company for $300,000 at the age of 21 and has founded three startups so far. Zhuang, the company’s other co-founder and CTO, is a New Jersey Institute of Technology graduate who has worked several years in pharmaceuticals and material science.
The founders are on a journey that could potentially re-engineer a wide range of food proteins, not only milk waste. Mi Terro’s first coin toss was in June 2019 when the milk-tee was launched on Kickstarter. The campaign was fully funded within the first two hours and the t-shirt was featured in international media such Bloomberg, Vogue, and Forbes.
In an interview with CompassList, Luo reflected on Mi Terro’s journey to date, the challenges encountered and what has yet to come, demonstrating how an optimized use of resources can drastically reduce human impact on the environment. Mi Terro had participated in the South Summit online conference earlier in October, where Luo pitched on behalf of the company in the Energy & Sustainability category.
This interview has been edited for length and clarity.
How was Mi Terro born?
It was when I noticed the buckets and buckets of spoiled milk at my uncle’s farm. That was when I first thought: why don't we give this bad milk a new life instead of it just being poured away? I went back to the US and I started doing a lot of research on what could be done with milk. At the same time, I was talking with my co-founder and friend Daniel Zhuang, who has a material science and chemistry background. We did a lot of research and found out that a milk protein can be spun into fiber or can be used as a very strong tool. That's when we started exploring and implementing the technology.
How does the technology work?
We call the first part Pro-Act: protein activation. This is where we extract the milk protein molecules from bacterially compromised cow milk. Once we extract the protein, we go through our second step called Sea-Re: self-assembly purification. Here, we purify bacterial proteins into a good protein that can be used to spawn fiber or packaging film. At this stage, we implement another technology called DFS: dynamic flow shear spinning. It’s a spinning process that turns the milk protein into textile fiber.
How long does it take for the whole re-engineering process?
The process of spinning the fiber can be actually done on the same day if the machines are close to each other.
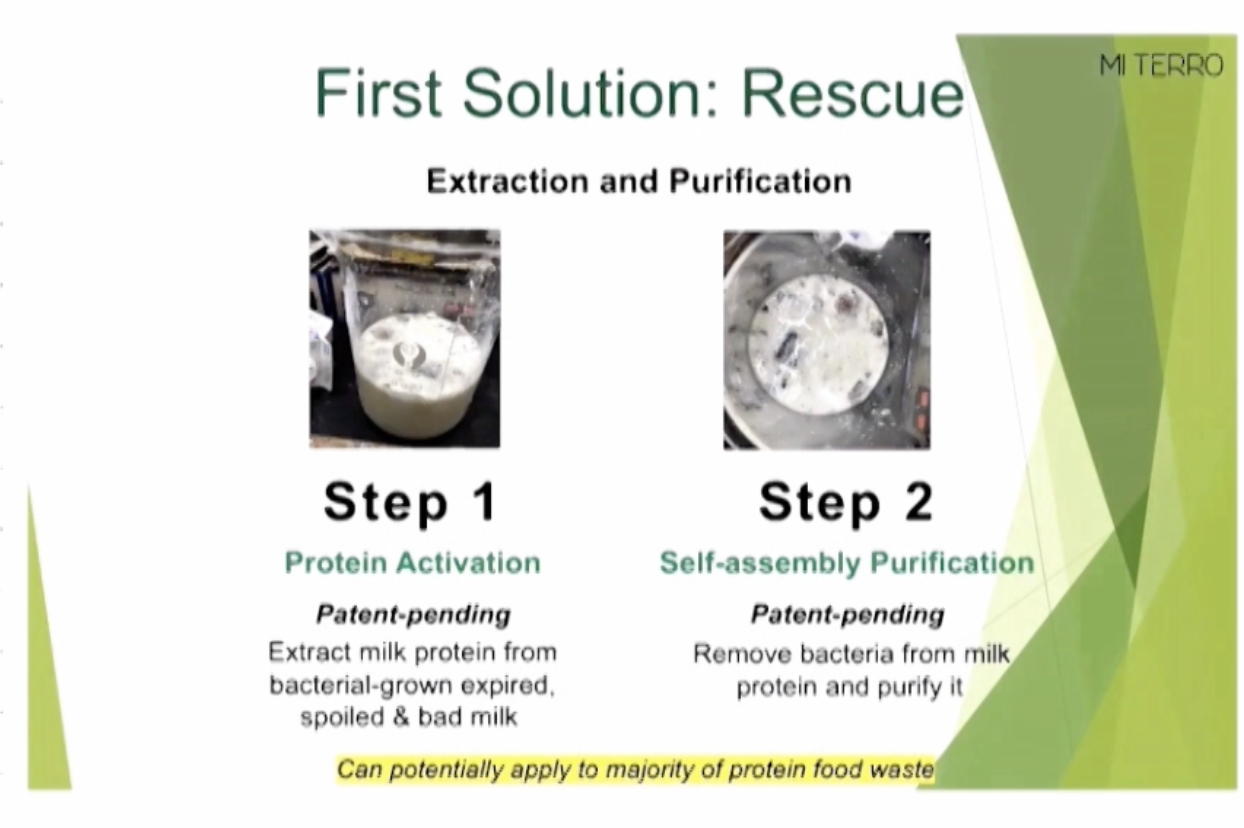
Where are your facilities?
Our R&D facility is in China, but we do also have farmers that implement our technology on their own farms to spawn the fiber.
Food waste contributes to around 6% of total global emissions, whereas the fashion industry is one of the most polluting. How are you making sure Mi Terro’s processes are eco-friendly and sustainable?
Reducing the carbon footprint is at the core of our business and that's why we are targeting food waste. Previously, food waste was undervalued. People haven’t spoken about it until recently. Now, other companies are trying to turn food waste into snacks, beverages, and edible products.
What happens to the foods that are inedible? These are the types of foods we target initially – the ones that are inedible for both humans and animals. So far, we are proud to say that we have upcycled over 10,000kg of milk waste, which translates into reducing about 49,000kg of carbon emissions in our environment.
We’re proud to say we have upcycled over 10,000kg of milk waste, which translates into reducing about 49,000kg of carbon emissions
I’d like to address another issue that people always bring up. Dairy has been portrayed in the media as evil. However, over the past 20 years, according to Dairy Farmers of America (DFA)'s data, the dairy industry has cut carbon emissions by 67%. That's a huge number.
We, together with scientists, are developing a great solution to reduce bovine methane emissions by feeding cows seaweed. We are finding more eco-friendly solutions to the dairy industry.
Have you partnered with research centers, universities, or any external advisors that have helped you build the technology?
We have two technical advisors. They are Chen Shengfu, a professor of Chemical Engineering and Technology at Zhejiang University in China, which is probably one of the best material science universities in the country; and Xie Jianping, Professor of Chemical and Biomolecular Engineering at the National University of Singapore.
What have been the greatest challenges you’ve faced in this phase?
Right now, we are developing a material that can replace plastic packaging. Currently, there's not a sustainable and cost-efficient bio-material solution. We're still using PVC. The reason why we don't have a good solution is that most of the material we use nowadays, such as POE or PBAT, can break easily. It doesn’t have the flexibility or stretchiness of PVC. That's one of the biggest challenges we have to overcome. We believe we have found a solution through the use of the protein molecules we have developed from different types of waste.
During the DFS (dynamic flow shear spinning) you separate casein (used for cotton fibers) from whey (used as a plastic alternative in packaging for cleaning products). At which stage will you’ll start looking into the development and commercialization of such a solution?
We are developing the packaging material right now. That's our new focus. We think that is a more urgent need for the entire world to reduce and replace plastic. We will start supplying our sample next year and commercialize in the next two to three years.
Which other materials are mixed with the spoiled milk to produce the t-shirt fiber?
We blend our fiber with viscose, another eco-friendly material. The average proportion of our milk protein fibre to viscose will be about 10% to 30%.
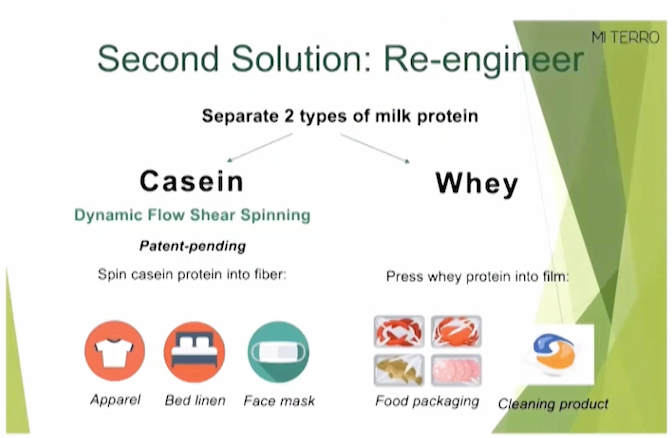
Who provides you with the excess milk and other dairy products?
We are speaking with two of the biggest dairy producers in China but I currently cannot name them. Next year, we're going to launch a pilot with DFA. They will be our main partners. We will also create a project with Danone, the details of which we cannot announce yet.
Have you considered working with supermarkets and food retailers to source new sources of raw material?
Most likely. However, in the US most of the milk waste that happens at the retail level goes back to the milk plants. That's why we think it is the best solution.
How are you going to scale your production volume?
We intend to move our production line to the American Midwest, where most of the dairy farms are.
If one glass of milk corresponds to five t-shirts, that’s quite a good return. Are you already in touch with fashion brands and textile companies?
We are collaborating with the Japanese company, Harada Corporation. They’ve purchased our new fiber and they are making it into an apparel line and are helping us to enter the Japanese market later this year. You will see a new apparel line made from this material at the end of the year. We have also signed Letters of Intent with other companies and we started shipping them our new fiber for testing.
Together with scientists, we are developing a solution to reduce bovine methane emissions by feeding cows seaweed
How much have you generated in revenue to date, and how much are you looking to generate this year?
To date, we have generated more than $110,000 overall. This has been a weird year for everyone and the projection has been drastically decreased, but our estimation is between $60,000 and $80,000.
Besides the environmental incentive, what are the advantages of using milk-protein fibers compared to traditional cotton fiber?
First, it’s the softness. Our fiber feels much softer than cotton and has a silky touch. Second, our price is lower compared with organic cotton. Organic cotton costs about $10 per kg whereas ours will cost $8 per kg, which makes it very appealing to the higher end markets such as baby apparel and the underwear market. The third will be that our fiber is made from food waste, which is a great selling point.
What is your business model? Have you started open sourcing the production process?
We will partner with suppliers and we will co-locate our technology on-site to turn the food waste into a powdered form. Once we have the powder form, it will be delivered to our centralized location to turn it into a final product that could be fiber or packaging film and then we will sell the final product to our clients.
Have you established partnerships/collaborations to support the R&D on the packaging material you are developing?
We are seeking partnerships with US’ Dole Food Company, and with Arla, from Denmark, which is one of the biggest dairy producers in the world.
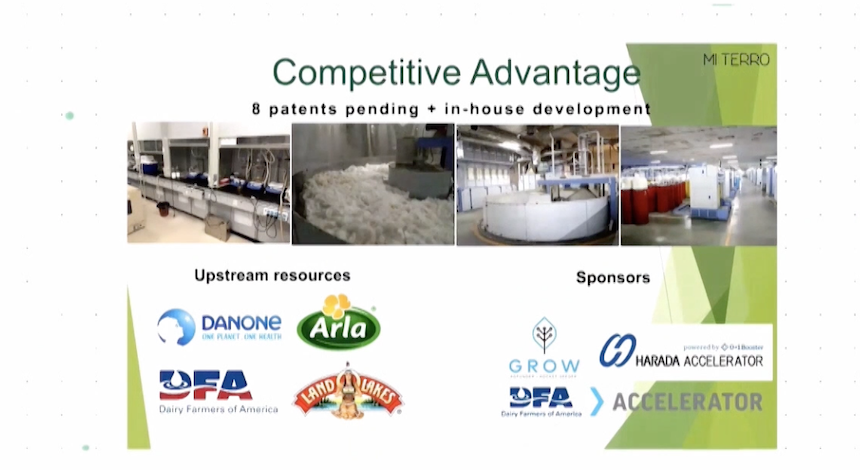
You raised $27,995 through Kickstarter and more recently you’ve been backed with $50k from Lair East Lab and $100,000 from an angel investor. Could you name the investor?
Yes, we have a Japanese angel investor, Yamamoto Sho. We will start raising our next round of investment next year, around February–March.
How has Covid-19 impacted your business?
Covid-19 has given people more knowledge about how much food waste the world generates. That's why there are more companies targeting this issue and we are very happy to see that the world is catching up. That gives us more opportunities to speak with our clients and to educate consumers on the importance of our work.
Where are you looking to expand in the near future?
The US has always been our first market. Then China and also the European markets. European countries consume a lot of dairy products, such as cheese, milk, yogurt, etc. That means there's huge production potential.
What food proteins will you investigate in the future to create plastic alternatives and cotton-alternative fibers?
We are going to test more plant-based products going forward, moving beyond dairy. One of the first ones will be distilled grains, the by-product of ethanol production. Right now, we are in a trial phase with Budweiser. We will look into soy as well. All of these have a huge production volume every year.